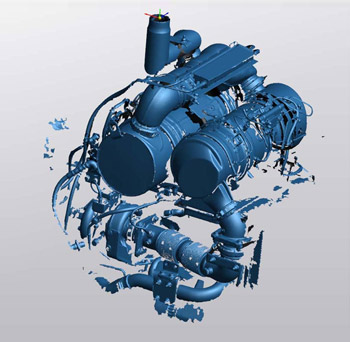

Remote Scanning – A New Way to Measure
One of the main challenges in manufacturing custom removable insulation blankets is obtaining accurate measurements. As a global company servicing clients world wide, Firwin is not always able to visit a site and take accurate measurements of the components to be insulated. We typically rely on CAD or 3D model drawings, photos, and sketches; but for more complex geometries where these are not accessible, getting proper measurements can be an issue. It can often come down to photos of a measuring tape over the components, a less-than-elegant solution which can sometimes be tricky to interpret.
Back in 2016, Firwin was contacted by one of its clients who needed a Komatsu Loader insulated. The geometry was quite complex, and getting the client to take the measurements was not realistic. Firwin and the client agreed to have a Firwin personnel fly out to the client’s site and take the necessary measurements.
Before proceeding, however, Firwin’s design engineer approached the client with a novel approach. “Rather than spending all that time and money on flying out one of our engineeers half way across the country, I proposed that we use remote scanning to provide us with a 3D image of the engine and exhaust”, said Jon Miles, Firwin’s Head of Engineering and Design.
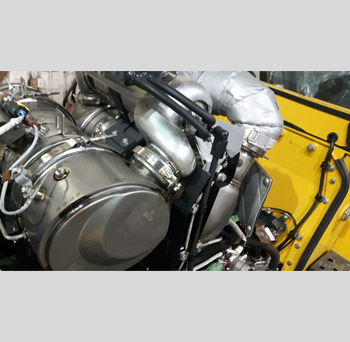
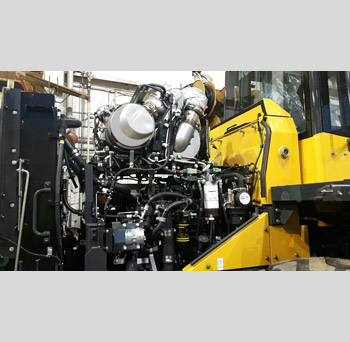
Firwin had actually been experimenting with remote scanning for a number of years, but until recently the technology was not yet at a state where remote scanning made sense. “The issue in the past has been how to process the scanned image in a manner that could be used as a model for designing blankets. In addition, the scanning technology itself was somewhat cumbersome. But recent advance in both software and hardware have made scanning quicker and easier; plus there is now third party software that assists in interpreting basic geometries, allowing us to take the scanned image and interpret it properly” , said Jon.
Firwin proposed hiring a local professional who would scan the components at the client’s site, and send the images onward to Firwin. A much more economical solution than flying out a Firwin engineer. The client agreed to try out this approach.
The result ? The photos speak for themselves. “We still had to run through a prototype to make sure the components fit properly, but that would be the case with any project of this nature”, noted Jon. “Overall, with the new hardware and software that is now available, this approach should become increasingly popular”.
For more information on applying remote scanning to your project, please contact Firwin.
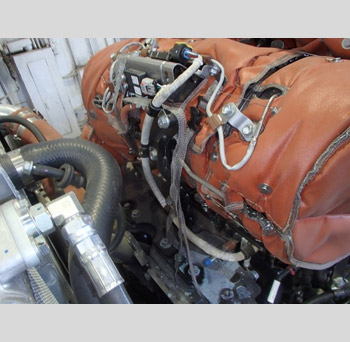
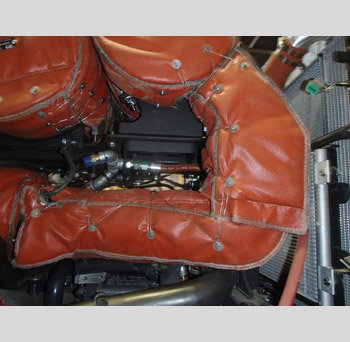
Other Articles : All About Elbows Firwin’s 1st Animated Video